Expert Guidance on What is Porosity in Welding and Exactly How to Resolve It
Expert Guidance on What is Porosity in Welding and Exactly How to Resolve It
Blog Article
Porosity in Welding: Identifying Common Issues and Implementing Best Practices for Prevention
Porosity in welding is a pervasive problem that commonly goes undetected till it creates substantial troubles with the honesty of welds. In this conversation, we will certainly discover the vital variables adding to porosity development, analyze its damaging impacts on weld performance, and talk about the finest practices that can be adopted to minimize porosity occurrence in welding procedures.
Usual Root Causes Of Porosity
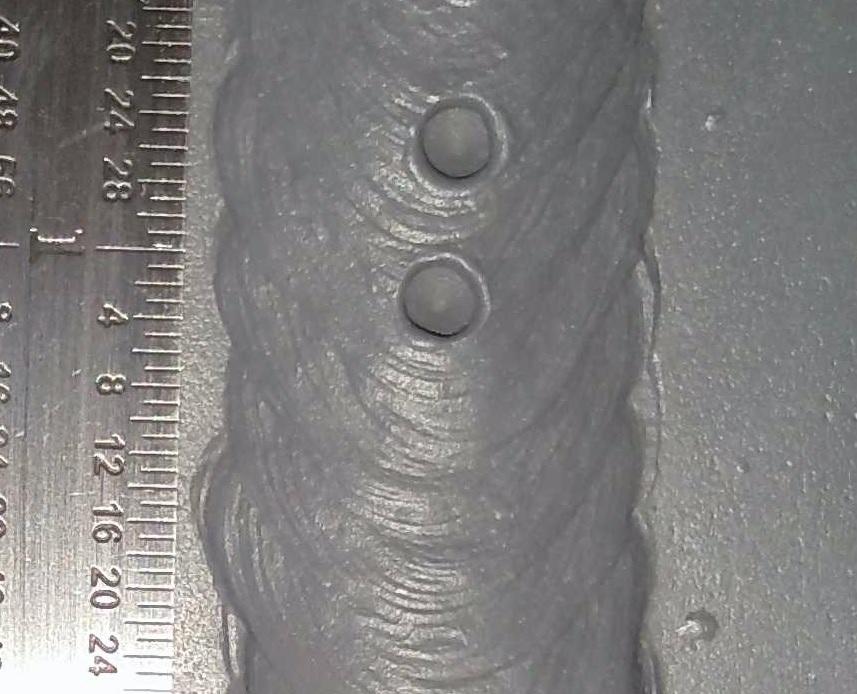
Utilizing filthy or wet filler materials can introduce impurities into the weld, contributing to porosity issues. To minimize these common causes of porosity, thorough cleansing of base steels, correct protecting gas choice, and adherence to optimal welding criteria are crucial practices in achieving top quality, porosity-free welds.
Impact of Porosity on Weld Quality

The presence of porosity in welding can dramatically jeopardize the architectural integrity and mechanical buildings of welded joints. Porosity develops voids within the weld steel, weakening its general strength and load-bearing capability.
Welds with high porosity levels tend to exhibit lower impact strength and decreased capability to warp plastically before fracturing. Porosity can hinder the weld's ability to efficiently transmit forces, leading to premature weld failing and possible safety and security threats in essential frameworks.
Finest Practices for Porosity Prevention
To improve the structural integrity and top quality of bonded joints, what certain procedures can be carried out to reduce the occurrence of porosity during the welding procedure? Porosity prevention in welding is important to guarantee the integrity and toughness of the last weld. One efficient practice is correct cleansing of the base metal, removing any kind of pollutants such as rust, oil, paint, or dampness that might result in gas entrapment. Ensuring that the welding tools is in excellent article source condition, with clean consumables and ideal gas flow prices, can likewise significantly lower porosity. Furthermore, maintaining a steady arc and controlling the welding criteria, such as voltage, current, and take a trip speed, aids create a regular weld pool that decreases the risk of gas entrapment. Making use of the appropriate welding strategy for the particular product being welded, such as changing the welding angle and weapon position, can better prevent porosity. Regular evaluation of welds and immediate removal of any kind of problems identified during the welding procedure are important methods to stop porosity and create high-grade welds.
Relevance of Correct Welding Techniques
Implementing proper welding techniques is paramount in ensuring the structural honesty and top quality of bonded joints, constructing upon the structure of efficient porosity prevention measures. Welding techniques straight influence the general stamina and check my source sturdiness of the welded framework. One vital element of appropriate welding techniques is maintaining the proper warmth input. Extreme heat can lead to raised porosity because of the entrapment of gases in the weld pool. Conversely, not enough warm may cause incomplete fusion, developing prospective powerlessness in the joint. In addition, utilizing the appropriate welding criteria, such as voltage, current, and take a trip speed, is crucial for attaining sound welds with marginal porosity.
Moreover, the selection of welding process, whether it be MIG, TIG, or stick you could try these out welding, must straighten with the particular demands of the task to ensure ideal outcomes. Correct cleaning and preparation of the base metal, along with picking the best filler material, are likewise essential components of skilled welding strategies. By sticking to these best practices, welders can reduce the danger of porosity development and generate high-grade, structurally sound welds.
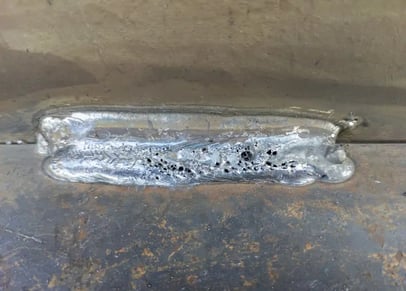
Examining and Top Quality Control Actions
Examining treatments are important to spot and protect against porosity in welding, making certain the stamina and resilience of the last product. Non-destructive screening approaches such as ultrasonic screening, radiographic screening, and aesthetic evaluation are commonly utilized to determine possible defects like porosity.
Post-weld assessments, on the various other hand, examine the last weld for any type of flaws, including porosity, and verify that it meets specified standards. Implementing a comprehensive quality control strategy that consists of complete screening procedures and evaluations is paramount to reducing porosity concerns and making certain the total high quality of welded joints.
Verdict
To conclude, porosity in welding can be a typical problem that impacts the top quality of welds. By determining the common root causes of porosity and applying finest practices for avoidance, such as appropriate welding techniques and screening procedures, welders can ensure top quality and trustworthy welds. It is important to prioritize prevention approaches to reduce the event of porosity and preserve the integrity of welded frameworks.
Report this page